When I turned 16 and qualified for my driver’s license, my parents and I entered into a mutually beneficial arrangement that I imagine is common in many suburban households: I could borrow a car to see my friends as long as I was willing to help out with tasks like taking my sister to soccer practice or running to the grocery store when they asked.
For that latter assignment, my mom would typically hand me a paper list and some cash or her debit card. I’d walk around Publix with a basket and tick items off the list. Flour, aisle 7. Bananas, produce. You get the picture, I probably don’t need to be explaining grocery shopping to you. But without fail, just as I’d finished the list and stepped into line, I’d get a text from my mom with some additional, crucial ingredient that she’d forgotten to mention previously. Sometimes, I’d miss the text and have to run back out after returning home. All that to say, I’ve never worked in construction, but I do understand how frustrating a change order can be.
In January of this year, the US Department of Transportation’s Volpe Center released its “Understanding Construction Change Orders” report, a 58-page document that identifies the common issues that cause change orders and suggests best practices to prevent them. It’s an excellent and comprehensive report, but a mere 33 words are dedicated to the role of ADCMS technology in reducing change orders. In this article, we’ll expand on that role and share specific examples of how an ADCMS can be one of the most important tools for change order reduction and management.
First, from the Volpe report:
“ADCMS streamlines interoperability, project management, submittal processes, communication, contraction administration, and approval processes to facilitate the execution of necessary change orders and accelerate communication that highlights potential issues that can become change orders.”
Now, let’s dive into the details.
Cost Estimation & Analysis
It may be an oversimplification to say that the better your estimate, the less likely your project will be to incur change orders, but it’s certainly accurate to say that it helps. The Volpe report points out that “errors, omissions, and overly optimistic assumptions during cost estimating and scheduling processes can result in budget overruns and schedule delays during construction.”
An ADCMS isn’t a cure-all to an inaccurate estimating process – you still need a team that understands methods like probabilistic risk-based estimating to take into account the range of project costs and schedule implications. But good estimates require data, and that’s where an ADCMS comes into play. This is especially true over time.
If you manage all of your projects within an ADCMS, compared to paper, spreadsheets, or other disparate data sources, you will have access to every change order you’ve ever approved in a searchable, exportable database. This data can allow you to draw conclusions on the most common change orders you encounter and how to prevent them. Are they mostly from things that are out of your control, like significant weather events? Or are they due to something like a consistent misevaluation of labor costs? The more projects you manage in an ADCMS, the more refined and actionable your insights will be.
Real-Time Project Tracking & Risk Mitigation
I have talked with many project managers who have said that their biggest change orders have come from a lack of real-time project data. Joe White, a project manager for Wolverine Engineers & Surveyors, spoke about how his inspectors would capture daily report information on printed templates and come back to the office once a month to square quantities and determine the accuracy of pay estimates. If something was off in the reports, any issues had the potential to snowball.
Take a story that was shared with me by Douglas Cade, County Engineer for Hancock County, Ohio. Cade receives inspection reports from his team in real-time via an ADCMS. On a recent subdivision inspection, an inspector reported an issue with the elevation of the road subgrade. As it turned out, the operator didn’t know how to read the grade stakes and undercut the road by two feet. Though that section of road needed to be adjusted and recompacted, Cade and his team were able to stop the operator before the entire street was built incorrectly – saving the county money from a substantial change order.
Simply put, access to real-time project inspection data from an ADCMS allows project managers to stop issues in their tracks. These errors may still result in a change order, like in Cade’s case, but real-time identification stops them from becoming financial catastrophes.
Communication, Collaboration, & Dispute Resolution
An unfortunate reality of traditional construction project management practices is that it often creates situations where the project manager and project contractors are at odds with each other. But the disputes that can arise over payment or other project issues are a remnant from the days of messy, paper-based record-keeping. An ADCMS prevents the sort of issues that lead to change orders from arising in two key ways:
- It provides the project manager and owner with a clear and explicit audit trail of work performed that takes precedence over conflicting versions of events
- It opens the door to a more collaborative relationship with contractors by inviting them into a shared hub for project data
As pointed out in the Volpe report, the Montana DOT employs a “Partnering Program” to produce “better working relationships between the DOT and contracting community to collaboratively address risk areas that can necessitate change orders.” An ADCMS can further support this collaborative relationship. For example, our own Appia software includes a feature called “Contractor Access” that enables contractor users to:
- View project items, item history, and high-level item details related to daily reports, change orders, and payments where the item is found
- See active punch list tasks, edit remarks, add attachments, and mark the task complete
In instances where change orders are necessary, an ADCMS helps ensure their accuracy. Take this example from our friend Joe White:
“The contractors that have learned to use it have had nothing but good things to say about it. We had a contractor run into some contaminated groundwater and soil. He went back and reviewed the inspector’s IDR, looked at the comments, and pieced together a change proposal for an extension of time because of the days associated with contaminated soil. He literally copied and pasted the comments from our IDRs into his supporting documentation.”
Of course, when disputes do occur, the comprehensive documentation of an ADCMS can serve to prevent change orders, as one CEI firm engineer shared:
“We had a project go to claim on a time issue. We had to see how much time impacted the contractor due to weather. With the search function in Appia, I can go in and say ‘weather days’ and quickly pull it up. That helped on the claim process.”
Process Standardization
Technology has great power to standardize the way we do things. I love movies and I have a terrible memory. My solution for this was to track every movie I watch, with a couple of notes and an overall rating. I tried a few things – a notebook, an Excel spreadsheet, my iPhone notes app – but these were hard to keep up with for one reason or another. When I found Letterboxd, an app that allows you to easily search, rate, and log movies in a diary, I never missed logging a film again. This article isn’t an ad for Letterboxd, but I do recommend checking it out. It’s free!
The Volpe report also recognizes the importance of standardization, stating that change orders often result from a “lack of internal and process standards and controls.” Look, it can be hard to get two people to follow the same process, let alone a whole team. You may have inspectors who have been doing their jobs the same way for decades mixed in with newbies who want to use their phones and the technology they’re intimately familiar with to get the job done.
An ADCMS puts up guardrails that enforce standardization. It can prevent many of the common process issues from occurring, including:
- Inconsistent documentation that leads to ambiguity or misinterpretation
- Variable communication methods that lead to differing information among different parties
- Unclear approval processes that make it difficult to track authorization and enforce accountability
- Delayed certifications or approvals for materials that can cause scheduling disruptions
Our own user community has shared several examples of how ADCMS usage helps them enforce process standardization. Jaime Kurten, Digital Design Manager for MSA, spoke about how MSA usually has a lot of interns to help with data entry. Having a consistent workflow with an ADCMS helps ensure the data is accurate and captured correctly by the intern team. “I think consistency in reporting was a high priority, to get that out of a field book or a PDF template and being able to capture that information in a more digital way,” she said.
Greg Fehrman, Principal Engineer at C+S Companies, shared how process standardization via ADCMS helps the team increase their capacity and reliability. “The advantage of using [an ADCMS] is that so many people are using it that when we bring on a new person specifically for a project, they’ve worked with it before. It helps with our capacity to perform.”
At the end of the day, change orders are an inescapable part of the construction world. There’s no tool in the world that can eradicate them completely, just like there is no tool in the world that would have prevented my mom from occasionally forgetting that we needed a carton of heavy cream until the last possible moment. Construction, in many ways, is about humans trying to control the uncontrollable. Nature. Human error. Divine circumstance. No, you can’t outright eliminate the things that cause change orders – but with an ADCMS, you can mitigate them, and take back what little control there is for the taking.
Authors
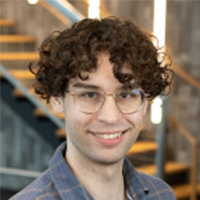
Nate Binder
Digital Marketing Manager
A proud graduate of Florida State University, Nate works with subject matter experts and sales professionals to produce targeted marketing collateral.